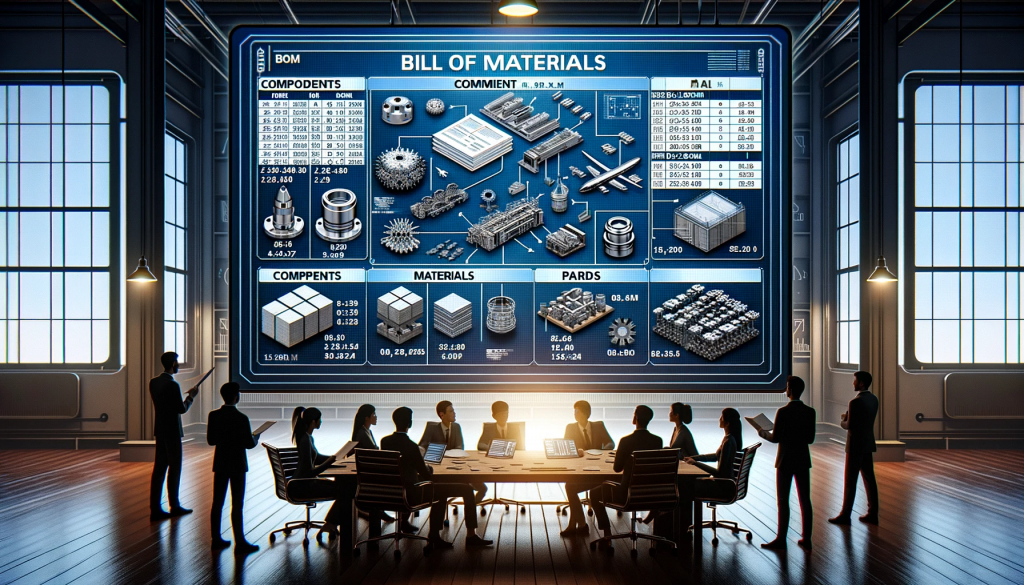
BOM is the secret behind every manufacturing company’s success. It enables companies to efficiently source thousands of parts and components to assemble the final product. As a manufacturer, a bill of materials is one of the most critical tools in your arsenal to optimize costs and streamline operations. In this article, you’ll get a quick primer on what exactly a bill of materials is, the different types you can create, and how leading companies utilize bill of materials to enhance productivity and profits. You’ll also discover some practical tips to help you overcome common challenges in managing bills of materials for your business.
What Is a BOM (Bill of Materials)?
A bill of materials or BOM is a comprehensive list of all the raw materials, assemblies, subassemblies, components, parts, and quantities needed to produce one unit of a product. It provides a complete, structured view of the product.
For manufacturers, the BOM serves as the foundation for production planning, costing, purchasing, scheduling, and supply chain management. It helps streamline operations by detailing exactly what materials and in what amounts are required to make a product. This allows companies to accurately calculate costs, ensure adequate inventory, and effectively plan production.
There are several types of BOMs used for different purposes:
- Engineering BOM: Created by engineers during product design. It details all the parts needed for a product.
- Manufacturing BOM: Used by production planners to specify materials and components required for production. It may differ from the engineering BOM.
- Costed BOM: Adds costing details like part prices, labor, and overhead costs. It is used to determine the total cost of a product.
- Sales BOM: Simplified version used by sales teams that only includes parts and materials visible to the customer.
Bill of materials is used across industries like aerospace, automotive, electronics, machinery, and medical devices. For example, an automaker would have a bill of materials for each vehicle model listing everything from large assemblies down to the smallest nuts and bolts. An electronics manufacturer would have bill of materials for each product specifying all electronic components, wires, casings, and packaging.
Managing BOMs does present challenges like keeping them up to date as products change, ensuring accuracy, and facilitating collaboration between departments. Following best practices like standardizing bill of materials formats, automating where possible, and maintaining clear communication can help overcome these challenges and maximize the benefits of bill of materials.
Types of BOMs and Their Uses
Manufacturers utilize various types of bills of materials for different purposes. The most common are:
Engineering bill of materials
Also known as E-BOM, this contains all the information needed to design and engineer a product including drawings, 3D models, and specifications of parts and subassemblies. They are living documents that evolve as the product design changes. They provide an overview of the product architecture and all the components required to build it. Companies use them to configure products for customers based on their unique needs and requirements.
Manufacturing bill of materials
Known as M-BOM, this transforms the E-BOM into a buildable design by specifying the exact parts, materials, and assemblies required for production. They break down the product into manufacturable chunks by optimizing the E-BOM for efficiency and cost-effectiveness. It contains crucial data such as part numbers, quantities, and the sequence of operations needed to construct the final product. They are used on the shop floor to drive automated equipment and ensure the right parts are used at the right time.
Costed bill of materials
The costed BOM, or C-BOM, builds on the M-BOM by adding pricing details for raw materials, components, and assemblies. It provides a complete cost breakdown of the product which helps with tasks like budgeting, estimating, and controlling inventory costs. However, they require frequent updates as material and component prices change. Maintaining accurate costed bills of materials can be challenging, but when done right, they give companies valuable insights into profit margins and cost optimization opportunities.
For selling products and growing the company, the most important is the sales bill of materials and configurable bill of materials. These two are mostly used in the sales process to configure products and in order processing to configure the order for production.
The key to effective bill of materials management is using the right types of BOMs for their intended purposes, keeping them up-to-date, and ensuring synchronization across departments. With the proper bill of materials strategy and tools in place, manufacturers can boost efficiency, reduce errors, and gain a competitive edge.